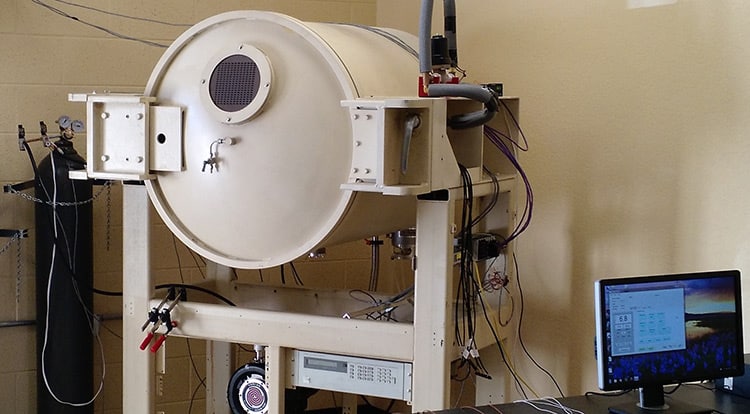
Thermal Space has a custom thermal vacuum chamber that is capable of testing components and subsystems from above ambient temperature to well into the cryogenic temperature range. Thermal vac testing is often used to simulated space environments or measure thermal properties of materials.
Thermal Conductivity/Thermal Conductance Measurements
Thermal Vacuum (or Thermal Vac) Testing
When testing components such as thermal straps and complete thermal subsystems, TSL has a custom thermal vacuum (thermal vac) chamber specifically designed for temperature and pressure control. Thermal vac testing is conducted using this chamber that is capable of being evacuated to 10-6 torr (roughly one-billionth of an atmosphere), well below the range where molecular convection heat transfer is significant. Temperature control at the thermal control plate can be maintained to within a degree over a range from -190°C to 180°C (80 K to 450 K).
Accurate and Proven Thermal Test Method
To measure the thermal properties of a material, heat (typically in the form of electrical heater power) is applied to one end of the component, while the other end is thermally anchored to a temperature controlled interface plate located within the thermal vac chamber. Our thermal vacuum chamber includes calibrated instrumentation that monitors and controls the pressure and temperatures necessary to make accurate measurements. Thermal conduction and thermal conductivity are calculated values resulting directly from the temperature measurements. We have developed our test document, TSL WI-004, to provide insight and detail on how thermal conductance is measured, calculated and reported.
The Thermal Space test procedure is based upon ASTM E1225-13, with data reduction in accordance with ASTM C1045 and E1970. This means that we measure heater power and heat conducted through the device under test (DUT) directly by the validation of heat flow through “meter blocks”, in accordance with ASTM E1225. The test setup minimizes parasitic heat leak (< 5%) and we account for any such losses to accurately determine heat being conducted through the DUT.
Cryogenic Thermal Vac Testing and Thermal Testing Over a Wide Temperature Range
Thermal Space specializes in cryogenic thermal vacuum testing. Thermal control of our heat sink interface (or cold plate) within the thermal vac chamber is achieved by liquid nitrogen or cold gaseous nitrogen for sub-ambient to cryogenic testing, and room temperature or heated gaseous nitrogen for ambient and above-ambient temperature testing. By monitoring and actively controlling the thermal control plate temperature, we can make thermal conduction measurements at temperatures between 80 K and 450 K, with 95% or better total accuracy. If you have special lower-temperature measurement needs, please contact us. Depending upon your test article, we have the capability of using either gaseous or liquid helium to reach 10 K and lower at the heat sink interface.
Thermal Vac Testing for Components, Devices, and Complete Thermal Subsystems
Our thermal vacuum chamber possesses enough thermal sensor channels that we can test multiple devices simultaneously, as well as larger-scale thermal subsystems. The approximate size limit for hardware tested in this chamber is 2.5-ft diameter by 3.5-ft length.
Virtually any hardware that will physically fit and mount to our temperature control plate can undergo thermal vac testing. The heat source is computer controlled through the power supply. The temperature control plate can be cooled or heated relative to ambient temperature. Thermal sensors attached to the test article can include RTDs, thermocouples, or a combination of both. In addition to standard test protocols, custom thermal test procedures can be written for measuring the thermal performance for a specific test sample, device, or complete thermal system. We work closely with our clients to be certain that you get the specific data and information that you want and need for thermal characterization.